Glass wool board is primarily made from glass fibers. These glass fibers are produced from molten glass, typically recycled glass, which is spun into thin strands or fibers using specialized manufacturing processes. These fibers are then bonded together using a binder material, often a thermosetting resin, to form a dense mat or board.
The manufacturing process typically involves the following steps:
1. Melting: Recycled glass is melted in a furnace at high temperatures, typically exceeding 1,200°C (2,192°F), until it becomes a molten liquid.
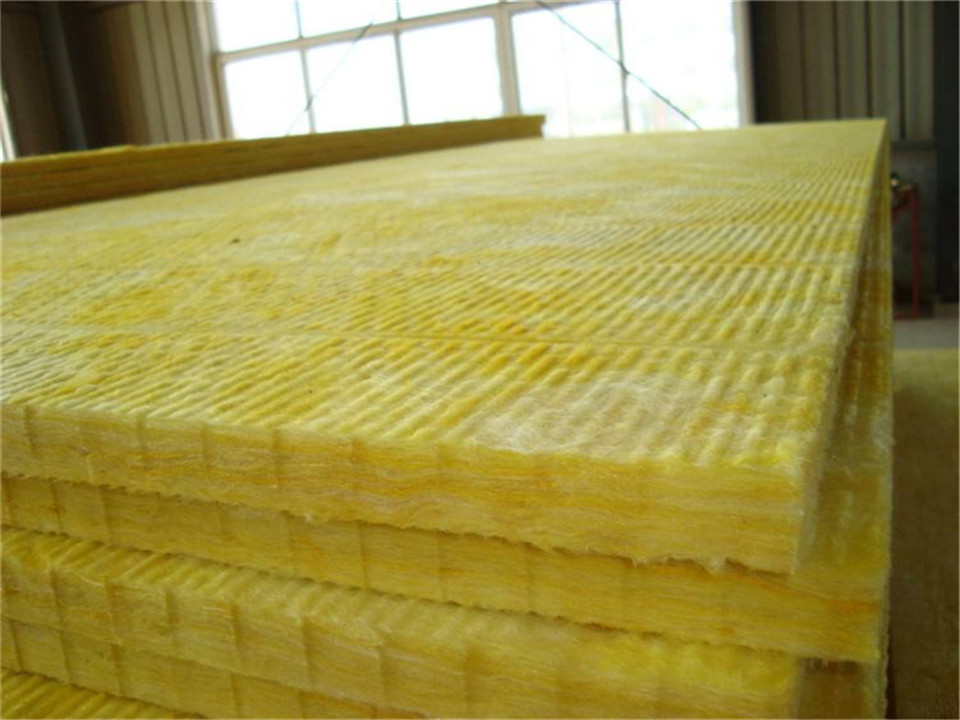
2. Spinning: The molten glass is then extruded through fine spinnerets to produce thin strands of glass fibers. These fibers are very fine and resemble wool, hence the term "glass wool."
3. Bonding: The glass fibers are collected and formed into a mat or blanket. A binder material, usually a thermosetting resin such as phenolic resin or acrylic resin, is added to the fibers to bond them together and provide structural integrity.
4. Curing: The binder is cured or hardened, typically through a heating process, to ensure that the fibers are firmly bonded together and form a solid board.
5. Cutting and Shaping: The glass wool mat is cut into boards or panels of various sizes and thicknesses to suit different insulation applications.
The resulting glass wool boards are lightweight, flexible, and have excellent thermal and acoustic insulation properties. They are widely used in residential, commercial, and industrial buildings for insulating walls, roofs, floors, and HVAC systems.